What are Data-driven Approaches in Advanced Process Control?
- picontrolsolutions
- Jan 25, 2024
- 3 min read
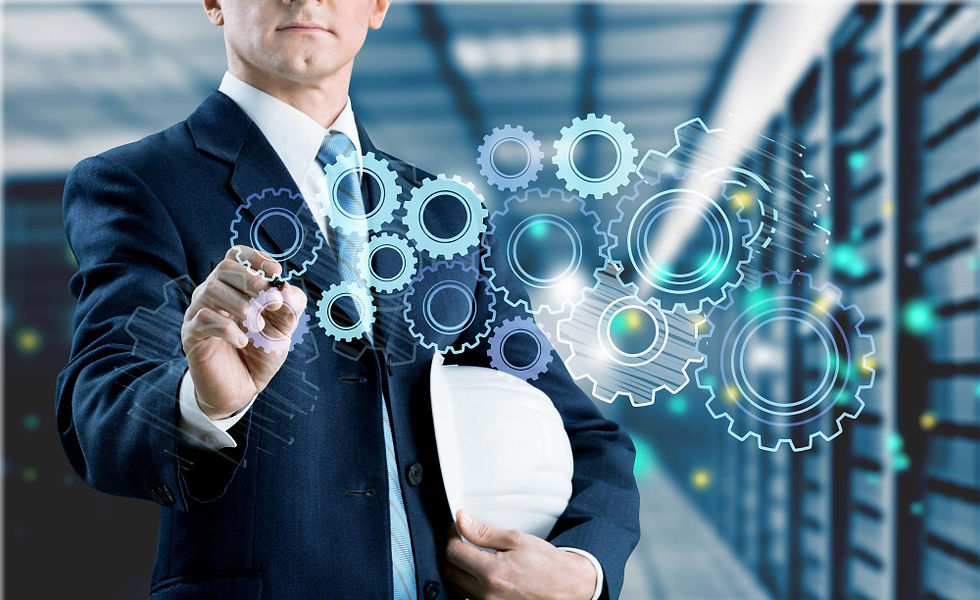
Data-driven approaches within Advanced Process Control (APC) stand at the forefront of industrial innovation, capitalizing on the transformative possibility of data analytics and machine learning. These processes comprise a sophisticated framework created to optimize complex industrial processes, upgrade efficiency, and ensure the trustworthiness and quality of outputs. In essence, data-driven APC illustrates a paradigm shift from conventional control techniques, introducing a vibrant and flexible approach that harnesses the wealth of data generated by modern manufacturing systems.
Significance of Data-Driven Approaches in APC:
The data-driven approaches in the method are complex but their possibilities are endless. Let’s explore them one by one.
1. Holistic Process Understanding:
At the core of data-driven Advanced Process Control is the ability to unravel the intricacies of process dynamics. Through detailed analysis of historical data, engineers acquire deep perspectives into the interrelationships among various variables, promoting a thorough knowledge of the system.
2. Model Construction and Complexity Handling:
Machine learning techniques take center stage in creating predictive models for intricate processes. These models, including regression, neural networks, and support vector machines, can capture non-linearities and time-dependent behaviors often inaccessible to traditional mathematical models.
3. Real-time Anomaly Detection:
Data-driven methods delegate real-time anomaly detection by setting baseline behavior through historical data analysis. This assertive identification of deviations enables swift intervention to thwart or reduce potential issues, enhancing overall system resilience.
4. Optimization Beyond Conventional Bounds:
Machine learning algorithms, integral to data-driven Advanced Process Control, transcend the limitations of traditional control strategies. By continuously assessing data, these algorithms specify optimal setpoints for process variables, tapping enhanced efficiency, decreased energy consumption, and superior performance.
5. Dynamic Fault Diagnosis:
The application of data-driven methods extends to fault diagnosis, enabling the system to recognize and categorize abnormalities autonomously. Training models on labeled datasets ensure a robust framework for identifying deviations from normal behavior.
6. Adaptive Control Strategies:
Data-driven Advanced Process Control embraces adaptability, allowing control strategies to evolve in response to changes in process dynamics or operating conditions. This adaptability ensures sustained optimal control performance over time, aligning the system with evolving requirements.
Components and Techniques in Data-Driven APC:
We’ve compiled the components and techniques of the process.
1. Historical Data Analysis as the Foundation:
The bedrock of data-driven Advanced Process Control lies in the meticulous analysis of historical process data. Engineers delve into trends, correlations, and patterns, extracting valuable insights that act as the basis for developing effective control strategies.
2. Machine Learning Models for Diverse Tasks:
Diverse machine learning models cater to specific process requirements. Supervised learning techniques, encompassing regression and classification, address prediction tasks, while unsupervised learning, including clustering and anomaly detection, aids in uncovering patterns and abnormalities.
3. Feature Engineering for Model Enhancement:
Feature engineering is a critical step involving selecting and transforming relevant variables to enhance the performance of machine learning models. This step ensures the extraction of meaningful information from raw process data, refining the predictive capabilities of the models.
4. Continuous Real-Time Monitoring:
Data-driven Advanced Process Control necessitates real-time monitoring of process variables. Advanced analytics devices constantly scrutinize incoming data streams, promptly detecting deviations and facilitating punctual rectifying actions.
5. Integration with Control Systems for Seamless Operation:
Seamless integration with overall control systems is paramount for unleashing the full potential of data-driven APC. This integration ensures a cohesive transition of insights from data analytics into actionable control strategies, fostering a closed-loop system for continuous improvement.
Applications and Benefits:
Check out the benefits of the procedure:
1. Proactive Predictive Maintenance:
Data-driven APC specializes in forecasting equipment failures by analyzing sensor data and spotting early indications of deterioration. It facilitates proactive maintenance, reducing downtime and extending the lifespan of critical assets.
2. Energy Efficiency Optimization:
Optimization algorithms sourced in data analytics recognize opportunities for energy savings. Fine-tuning setpoints and control strategies leads to more efficient functioning, reducing power consumption and operational costs.
3. Enhanced Quality Control:
Machine learning models contribute significantly to quality control by predicting and preventing deviations that may impact product quality. It ensures consistent compliance with desired specifications.
4. Heightened Process Reliability and Safety:
Data-driven APC improves process trustworthiness by detecting likely issues before they aggravate them. Continuous tracking and quick response to anomalies prevent safety incidents and reduce the risk of equipment failures.
5. Continuous Improvement Through Adaptability:
The adaptive nature of data-driven approaches allows for constant improvement. The system, learning from new data and evolving operating conditions, autonomously updates control strategies to optimize performance over time.
Conclusion:
Data-driven approaches within the process herald a new era in industrial automation, leveraging data analytics and machine learning to unlock unprecedented efficiency, reliability, and safety levels. The adaptive nature, continuous learning, and dynamic responsiveness to data make data-driven APC a cornerstone for the future of intelligent and autonomous manufacturing processes. While challenges persist, the potential benefits in terms of optimization, predictive capabilities, and overall process enhancement render the integration of data-driven APC compelling and essential for the evolution of diverse industries. If you're looking for a top software company developing Advanced Process Control, look no further than PiControl Solutions LLC. Make your business adaptable and productive.
Comments